Our Services
Closed System Chemical Cleaning, Flushing and Dosing
Closed-system chemical cleaning, flushing, and dosing are essential processes used in various industries to maintain the performance, efficiency, and safety of their equipment. These processes involve the use of chemicals to remove dirt, scale, and other contaminants from closed systems such as pipelines, heat exchangers, and boilers. Chemical flushing is used to remove any residual debris or contaminants from the system, while dosing involves adding specific chemicals to the system to prevent corrosion and scaling. These processes are critical for maintaining the reliability and longevity of closed systems and ensuring that they operate at optimal levels.
When do I need pre-commission cleaning and analysis of a closed water system?
What do we do?
Upon receiving the client's specifications this is then reviewed against BISRIA BG 29/2012 guidelines along with schematic drawings of the water system installation.
Our experienced BISRIA-qualified engineers will attend the site prior to the work commencing to carry out a microbiological sampling from the mains supply and if possible the system to be flushed to determine flushing and dosing requirements.
Following the initial visit and microbiological sample results, a site-specific method statement based on the client's bespoke requirements is prepared and sent out to the client for approval. This identifies the responsibilities of the client and WMS
WMS can also obtain consent to discharge license from the local water board, allowing for the disposal of system water and chemical used during the process
Prior to chemically cleaning the system, WMS technicians can carry out the pre-treatment of the water used for pressure testing. This provides early-stage protection against the microbiological activity, biofilm development and corrosion
If it has been noted from initial sampling that the water quality and system condition is microbiologically contaminated, a biocide wash is undertaken, targeting the removal of biofilms and eliminating bacterium such as Pseudomonas, which can cause severe illness if exposed
A high-velocity dynamic flush of the closed system removes any large debris from the system*, flushing to drain until the system water runs clear.
*Debris from the manufacture, installation and early-stage corrosion particulates are lifted from the system by achieving specified flow rates, set out by BG 29/2012 and are dependent on pipework size. The flow rates are witnessed and recorded by WMS for future reference
A nitrite or molybdate-based cleaning agent is circulated throughout the closed system for 24 hours, removing oil, grease and flux residue, dispersing iron oxide particulates and preparing all metal surfaces for chemical dosing by passivation – if aluminium is part of the construction of the system then a multimetal agent will be used.
During the chemical cleaning process, iron levels within the system increase as iron is removed from the internal surfaces of the pipework. The cleaning procedure is complete once these levels begin to plateau. The length of this process varies dependent on the levels of iron oxide present within the system prior to starting the works
The closed system is then refilled with chemically treated water containing corrosion inhibitors and biocide. Chilled systems may be dosed with Glycol for frost protection
Terminal units present on the closed system, i.e. radiators, radiant panels, chillers, air handling units etc, which have been isolated from the flushing procedures to protect sensitive material and equipment, are back flushed using the inhibited water present in the main circuit
Following the backflush, the levels of inhibitor and biocide are re-tested using a photometer on site and if necessary are topped up to achieve specified levels
The system is sampled and analysis is carried out to ensure the effectiveness of the chemical cleaning process. Tests include; Pseudomonas, sulphate-reducing bacteria, TVC, nitrite-reducing bacteria, pH, electrical conductivity, total hardness, total alkalinity, total suspended solids, chloride, sulphate, nitrate, soluble iron, total iron, total molybdenum, nitrate, total phosphate, dissolved oxygen, total dissolved solids and copper
Upon completion, WMS issue the client with a detailed report and certificates, as well as microbiological sample analysis results from WMS UKAS accredited laboratory to satisfy all commissioning requirements
WMS technicians will undertake regular monitoring visits, as agreed as part of the client's water treatment regime, carrying out chemical analysis of the system water and testing for inhibitor levels, and where applicable Glycol levels. Microbiological testing is also continued to ensure bacteriological activity is within acceptable limits
INFORMATION
Useful information about Legionella and what it means for your business.
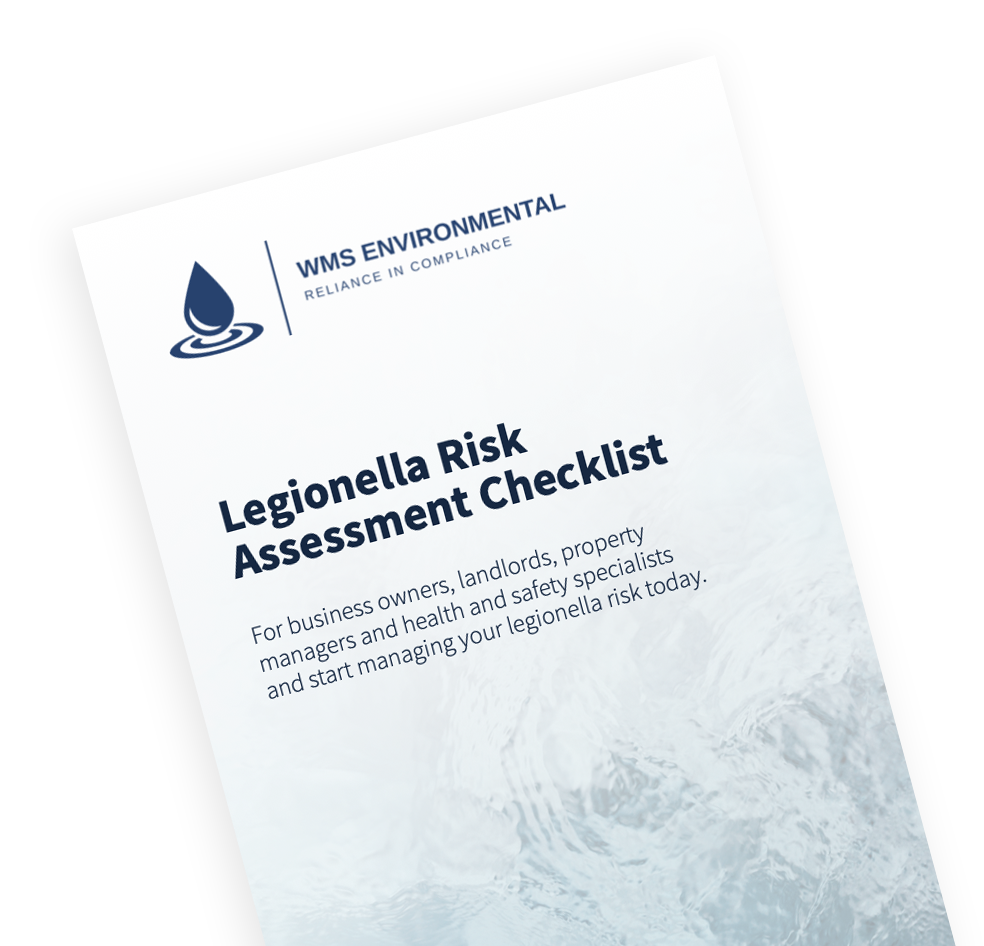